Lorsqu’il s’agit de lancer un projet, qu’il soit le premier d’une série, l’ajout d’une usine ou le transfert d’une installation existante, l’étape de lancement est primordiale. Chaque détail non anticipé lors de la phase initiale peut devenir un obstacle majeur à la réalisation des objectifs de performance, entraînant potentiellement des augmentations significatives des coûts d’investissement et de production.
Afin de garantir le succès du projet, il est impératif de mobiliser les ressources nécessaires en termes de temps et de compétences : une planification rigoureuse, ambitieuse et précise pour garantir le succès du projet.
Le but du cadrage de projet est de définir et d’objectiver un système industriel. Tous les livrables de ce premier jalon ont pour objectif de challenger les hypothèses prises et de donner une direction claire aux équipes impliquées.
I. Greenfield ou Brownfield
Faut-il lancer un projet greenfield (terrain à bâtir) ou opter pour un brownfield (bâtiment déjà existant, avec ou sans modification) ?
Chaque option à ses avantages et ses inconvénients :
Greenfield
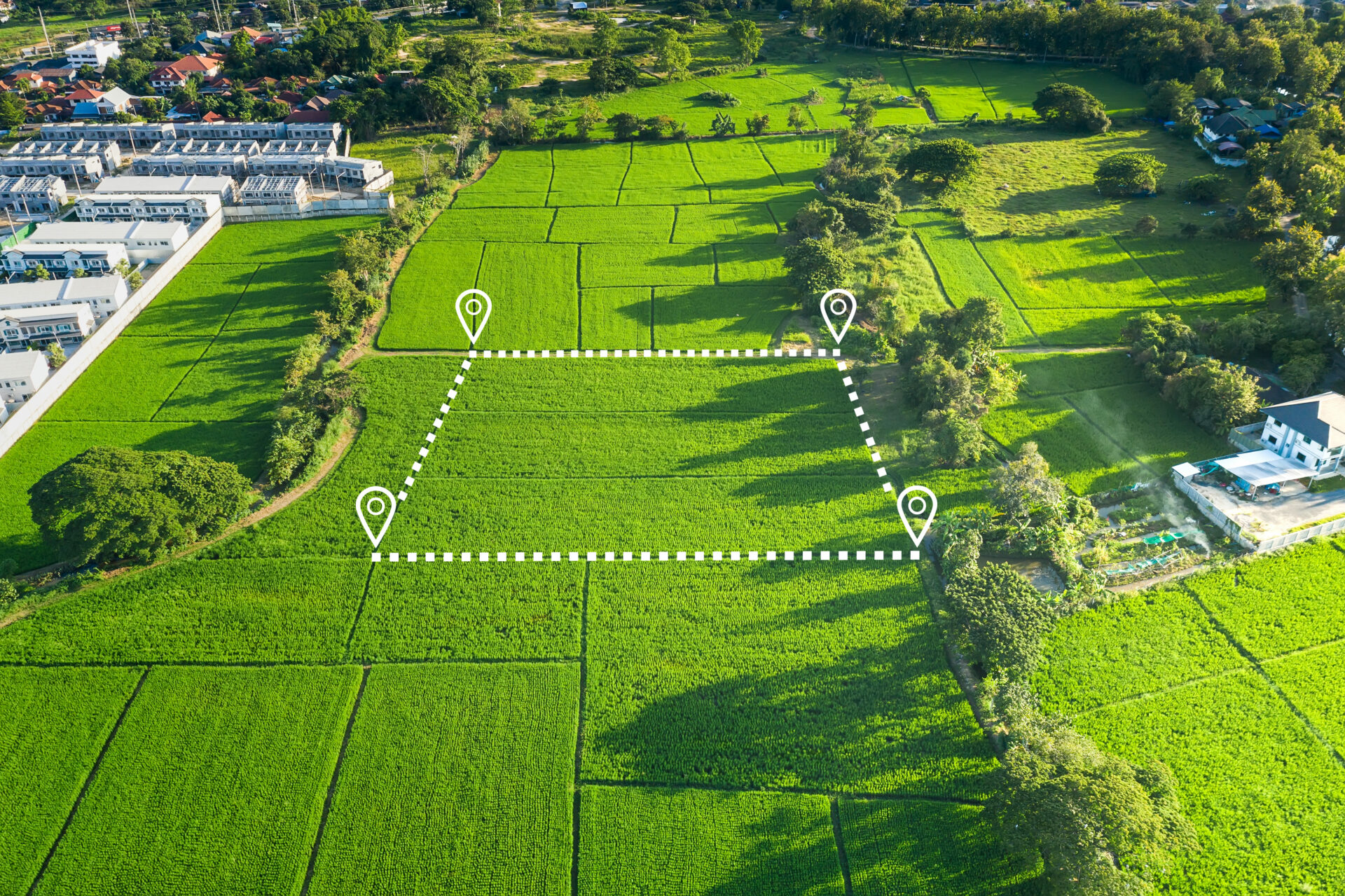
+ Avantages
- Liberté de conception : Conception et mise en œuvre de l’usine à partir de zéro, sans contrainte imposé par des structures existantes.
- Flexibilité : Possibilité d’adapter l’usine à ses besoins spécifiques avec moins de limitations.
— Inconvénients
- Coûts initiaux plus élevés : La construction et l’équipement d’un nouveau site peuvent être plus coûteux.
- Temps nécessaire : Le projet peut prendre plus de temps car tout doit être créé à partir de zéro.
Brownfield
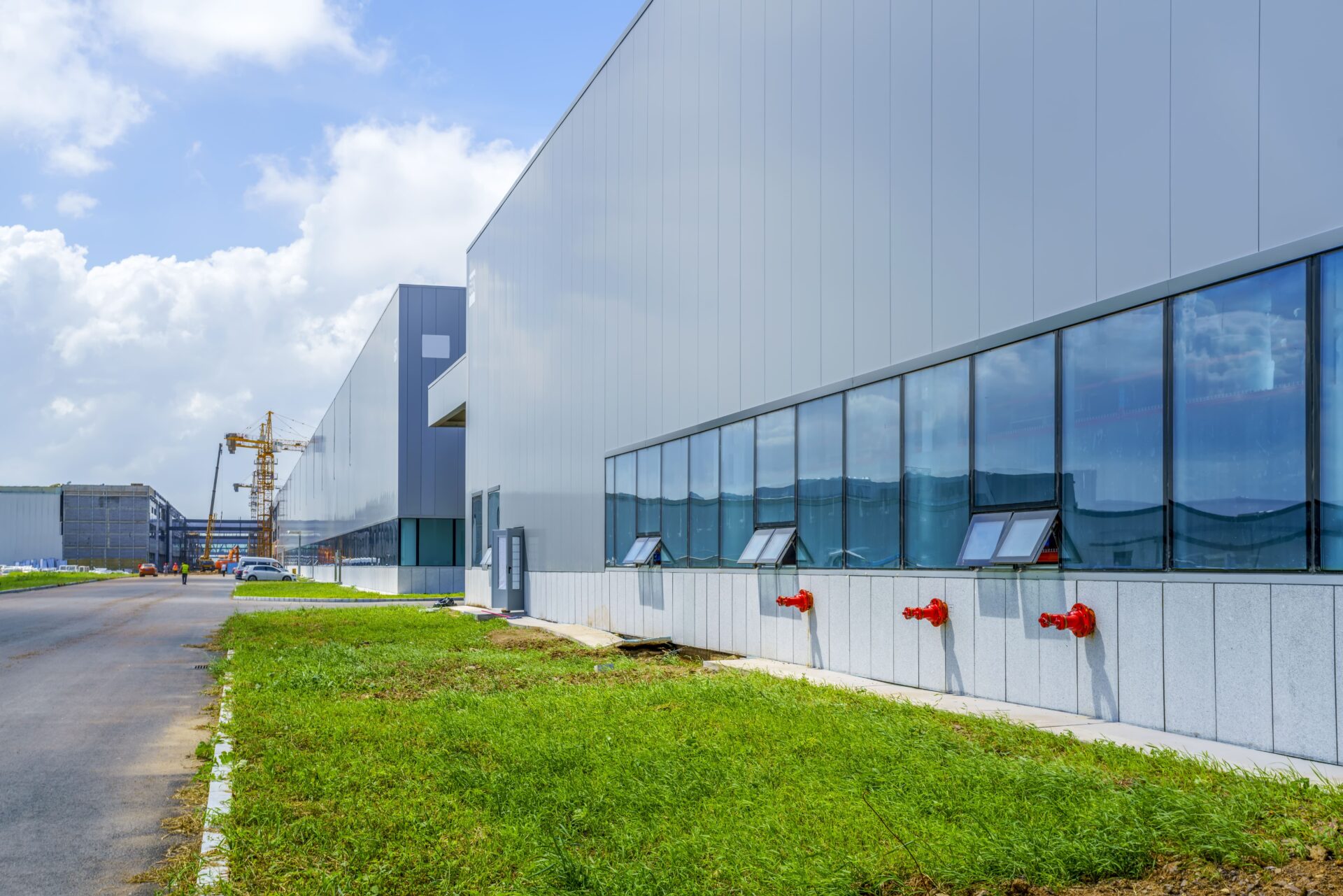
+ Avantages
- Réduction des coûts : L’utilisation d’une infrastructure existante permet d’économiser sur les coûts de construction.
- Gain de temps : Possibilité de démarrer plus rapidement en réutilisant les installations existantes.
- Localisation : Les sites brownfield sont souvent situés dans des zones déjà bien desservies.
— Inconvénients
- Contamination potentielle : Risque de pollution du sol ou de l’eau due à l’activité précédente.
- Limitations de l’infrastructure existante : Travailler avec un bâtiment existant peut fortement contraindre les flux et les opérations de production, ou bien faire monter les coûts de manière très importante si des travaux sont à entreprendre.
II. Choix du terrain
Le choix du terrain repose sur plusieurs questionnements qui doivent être méticuleusement posés :
- L’emplacement est crucial pour la réussite du projet :
Il faut tenir compte de la proximité des infrastructures de transport, des réseaux électriques et de communication, mais aussi de la dynamique du bassin d’emploi (main-d’œuvre) ou encore de la présence d’écoles et d’universités. Bien entendu, il faut aussi connaître les règles d’urbanismes applicables au terrain. - Géométrie du terrain :
Les dimensions sont importantes, mais sa géométrie l’est tout autant. Une forme exotique peut restreindre les flux de circulation et l’aménagement des zones, entraînant une augmentation des voies de circulation et une diminution des espaces verts obligatoires selon les règlements PC/ICPE. - Implantation du site dans son environnement :
Il faut prendre en compte le voisinage : habitations, usines, voies ferrées, aéroports et voies d’eau. Tous ces éléments peuvent avoir un impact direct sur l’activité ou le projet industriel (notamment contraindre les travaux en raison de mesures compensatoires).
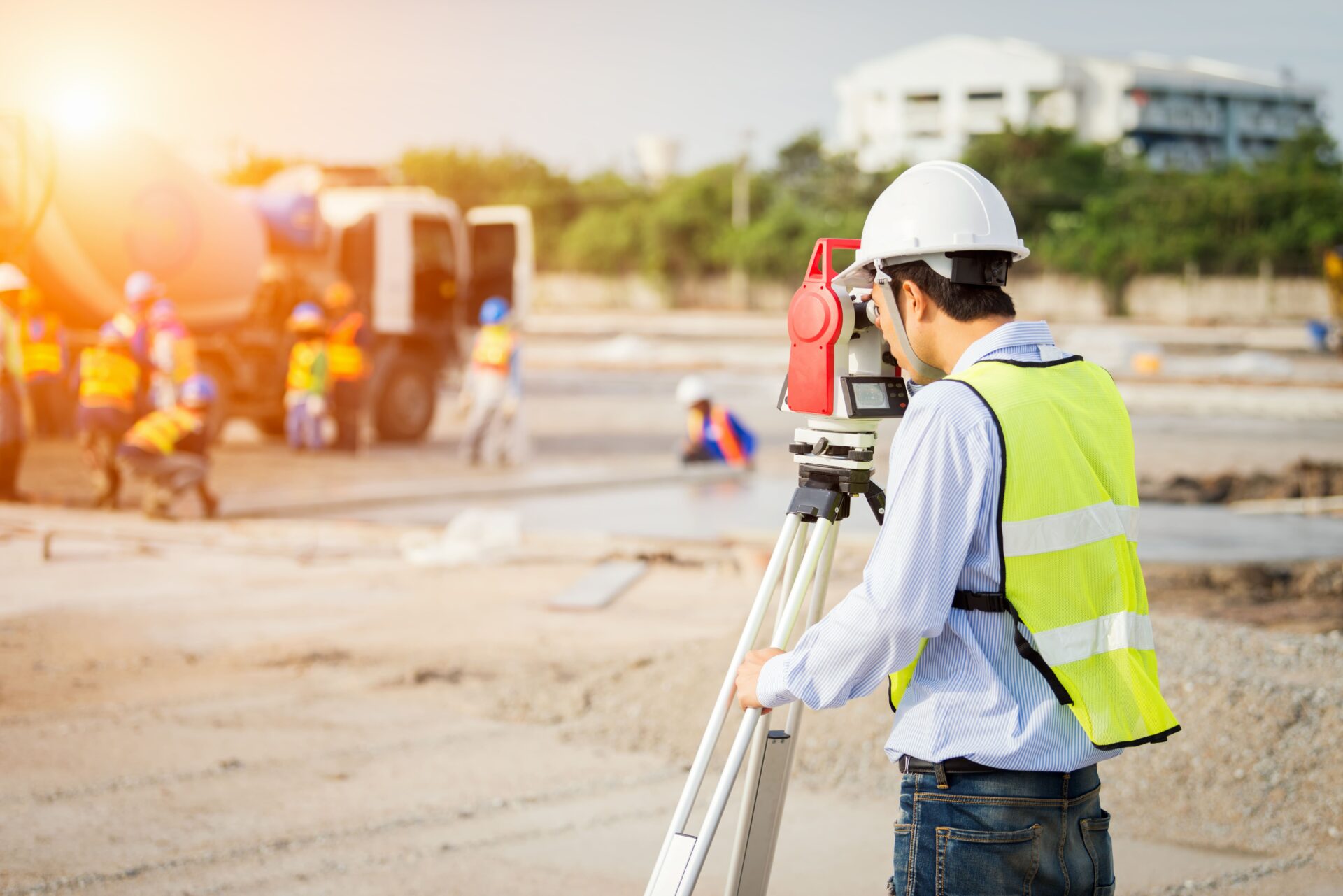
III. Zones de process
Aborder la zone de process implique de prendre en considération divers éléments critiques pour la réussite du projet notamment en rapport avec la production :
- Définir le mode de production
Il doit être choisi en fonction du produit, de sa diversité, des cadences de production… - Automatiser ou non sa production
Le choix d’automatiser peut avoir plusieurs motivations : diminuer les OPEX (Operational Expenditures), fiabiliser le process pour augmenter la qualité, soutenir une cadence forte, diminuer la pénibilité de certaines opérations ou palier à une tension de recrutement. Mais l’automatisation a aussi ses inconvénients : augmentation de l’investissement, diminution de l’adaptabilité du process et un besoin de maintenance accrue. - Bien connaître son process pour mieux l’optimiser
Le synoptique process consiste à définir les temps de chaque opération et de chaque transfert inter-postes pour identifier les points de congestion. Cela permet d’ajuster le processus si nécessaire et de déterminer l’implantation des différentes zones ainsi que les contraintes spécifiques requises (humidité, température contrôlée, aérations…). - Implantation 2D ou 3D
À ce stade du projet, le but est de valider un cadrage et des principes d’implantation. Par conséquent, sauf process complexe nécessitant une validation par la 3D, des plans 2D suffisent pour limiter le coût de l’étude. En revanche, si des personnes extérieures au monde industriel doivent valider le projet (investisseurs ou institutionnels dans le cadre d’une demande de subvention publique), une visualisation 3D peut avoir plus d’impact dans la prise de décision.
IV. Zones logistiques
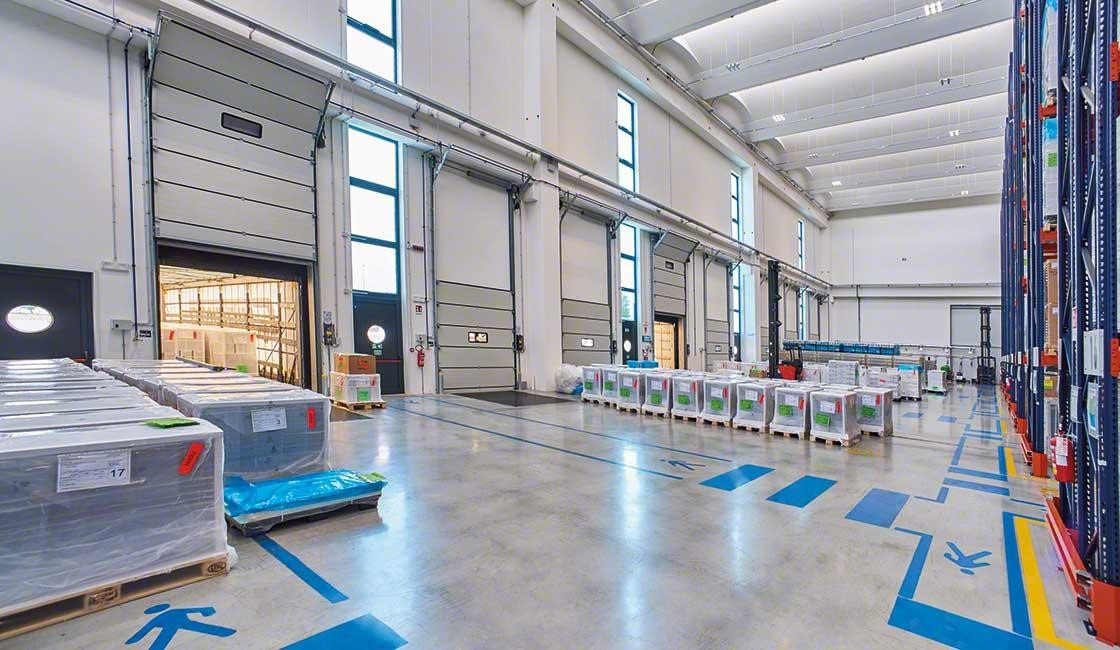
Pour aborder les zones logistiques, il est essentiel de comprendre l’importance stratégique de leur organisation et leur impact sur l’efficacité opérationnelle globale.
- Quel mode de stockage ?
Au sol, en hauteur, en grande hauteur ? Conventionnel ou automatisé ? Cela va dépendre de beaucoup de paramètres :
- Le type de produits stockés (nature, dimensions, conditionnement, denrées périssables ou non, froid positif ou négatif, produit dangereux, zone sous atmosphère à risque explosif ATEX – ATmosphères EXplosibles -)
- La stratégie LIFO (last in, first in, first out) ou FIFO (First in, First out)
- L’agilité nécessaire (rapidité du processus, juste-à-temps…),
- Les quantités à stocker
- La cadence de l’activité logistique
- Bien définir ses flux :
Les flux à l’intérieur des zones logistiques, les interfaces avec le process et les approvisionnements en bord de ligne, le retour des déchets, les flux extérieurs, le nombre et le type de quais, les zones d’attente camion, les voies de circulation.
- Quel mode d’approvisionnement en bord de ligne ?
Tout dépend du mode de production : en ligne, en continu, par batch…
De manière générale, il faut définir sa stratégie en fonction :
Des temps d’ouverture des différentes activités process et logistique (1×8, 2×8, équipe weekend, VSD, désynchronisation entre équipes logistiques et équipes process…).
Du mode d’approvisionnement des fournisseurs (cadences et volume de livraison)
Du capacitaire de stockage bord de ligne et des zones magasin
Le mode d’approvisionnement ainsi défini, permettra de dimensionner les équipements nécessaires (car à fourche, petit train, AGV/AMR) et de consolider un estimatif CAPEX/OPEX, mais également de définir les surfaces aux interfaces [bords de ligne avec un stockage par batch ou avec meubles gravitaire d’approvisionnement en flux continu, meuble de kit attitré à chaque produit…].
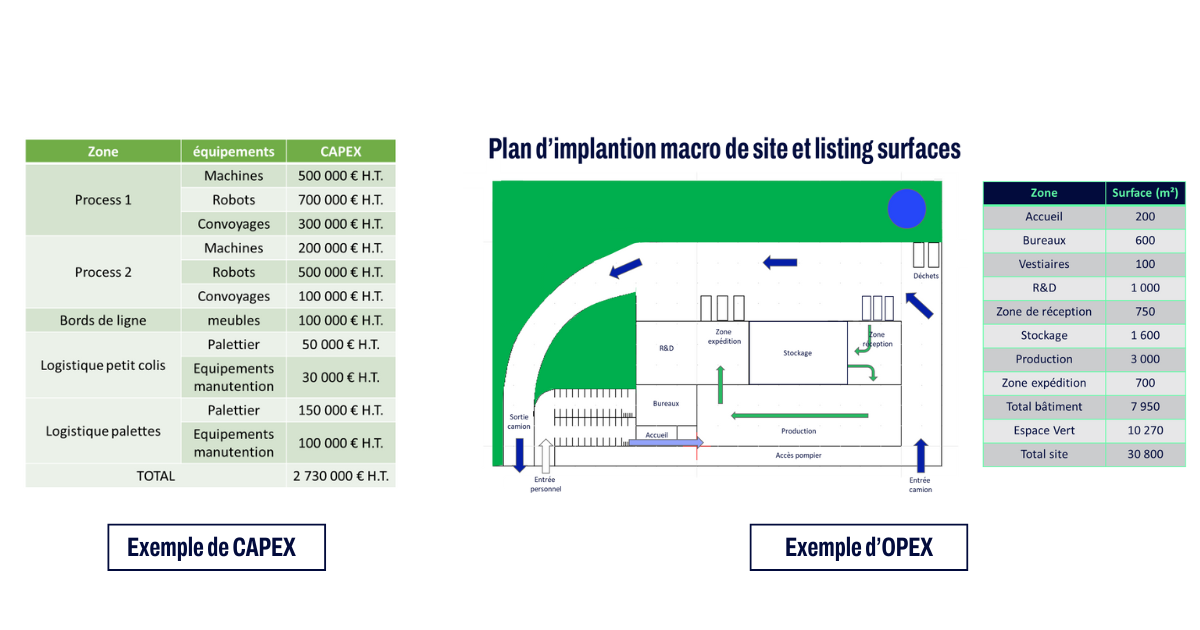
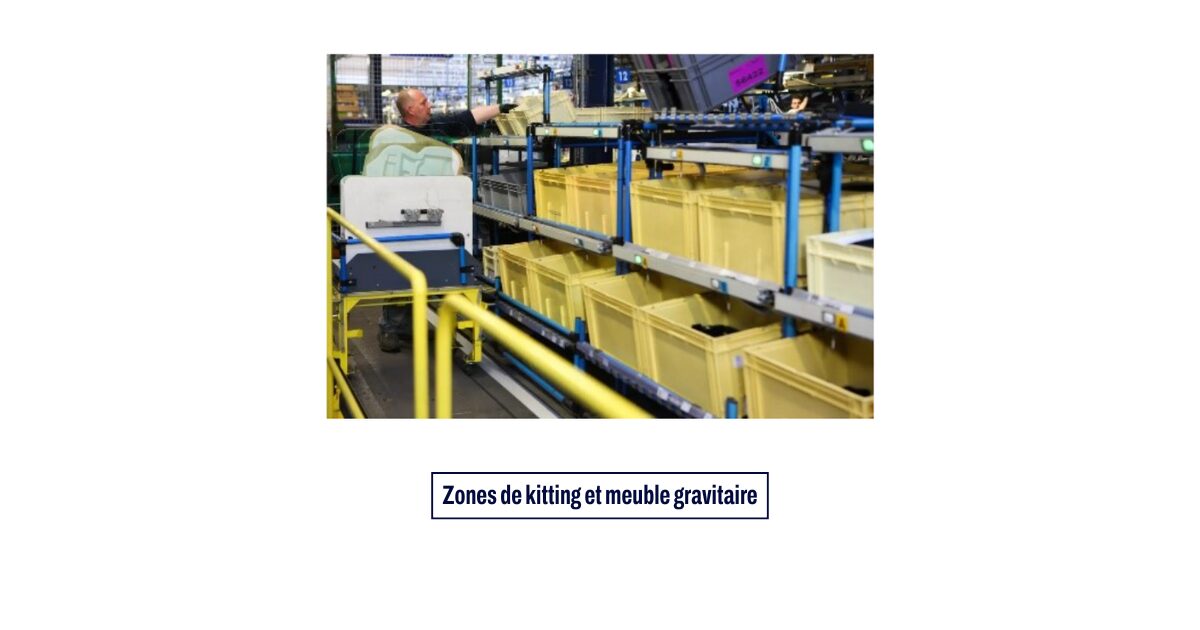
V. Organisation générale des surfaces et implantation
Pour explorer l’organisation générale des surfaces et des implantations, il est primordial de comprendre comment ces éléments structurels influent sur la fluidité des opérations et sur la performance globale du projet.
- Une usine pour quel avenir ?
Le volume de production est la première donnée d’entrée de tout projet industriel. En effet, le but est de bâtir un outil permettant de se projeter dans 5 à 10 ans. Le système industriel mis en place doit également pouvoir être prolongé sur un horizon plus lointain : il est donc pertinent de réfléchir aux futures extensions et de concevoir les bâtiments et les équipements les rendant possibles. Un bon système est un système performant, mais aussi scalable. - Transfert de votre outil :
Si le projet industriel vient en lieu et place d’un système existant (que cela soit sur le même site ou sur un autre site avec transfert d’outils de production), la question de la continuité d’activité va se poser. Un lissage de la production afin de garantir les ventes des produits sans impact pour les clients finaux est-il possible ? La méthode de continuité d’activité va dépendre de vos produits, et notamment de leur caractère périssable.
Plusieurs possibilités sont envisageables :
- Surproduire avant l’arrêt de l’outil actuel : Cela nécessite d’avoir un système en mesure d’augmenter sa capacité de production (par exemple en étendant momentanément les heures d’ouvertures) et surtout de pouvoir stocker tous ces produits excédentaires, en interne ou en externe.
- Concevoir la stratégie de transfert par phase : en déménageant les zones petit à petit pour minimiser le temps unitaire de transfert, bien que cela puisse complexifier la production durant la transition.
- Doubler certains process : pour assurer une production minimale quelle que soit l’étape de transfert, même à une cadence réduite.
- Minimiser le temps de démarrage du nouvel outil : en anticipant les tests de tous les équipements le permettant (montage à blanc chez les fournisseurs ou dans des zones transitoires, lancement d’une simulation de flux pour définir les paramètres d’utilisation à la performance nominale prévue, etc.).
- Externalisation temporaire d’une partie du process le temps du transfert.
- Optimisation des flux internes :
Rationaliser l’implantation du bâtiment en réfléchissant aux flux des hommes et des marchandises qui ne doivent pas se croiser. Un flux parfaitement organisé, en plus d’être sécurisé, permet de gagner du temps et garantit une implantation optimale et une performance accrue. - Zones non dédiées à la production :
Ne pas oublier d’ajouter les zones bien dimensionnées pour les bureaux, les vestiaires, les locaux sociaux, les zones de vie, les zones techniques, le bassin de rétention, etc... - Attention aux flux de véhicules sur site :
Il est important de séparer les flux de marchandises (camions) et les flux des véhicules personnels (collaborateurs ou visiteurs), et surtout d’éviter les croisements de flux sur site. Vérifiez sur le PLU (Plan Local d’Urbanisme) qu’il est possible d’avoir plusieurs entrées/sorties sur la parcelle, sans quoi il sera difficile de séparer ces flux.
VI. Normes et règlementations
Avant d’entrer dans les détails de normes et de réglementations, il est crucial de comprendre leur impact sur la conception, la mise en œuvre et l’exploitation du projet, ainsi que sur la conformité légale et la sécurité des opérations.
- Normes en vigueur :
Respecter les normes de sécurité, d’accessibilité et de construction pour garantir la conformité du bâtiment industriel dans la durée. - Règles d’urbanisme et règles environnementales :
Lors de l’implantation de l’usine, il est crucial de respecter les règles d’urbanisme (PLU, permis de construire) et de bénéficier d’un accompagnement pour les aspects environnementaux du projet (études ICPE, sécurité incendie…) - Études et enquêtes liées à l’implantation :
Suivant la zone d’implantation et l’activité de l’entreprise, différentes études et enquêtes peuvent être nécessaires : pollution des sols, géotechnique, faune et flore, topographie, archéologie… Ces études peuvent nécessiter un temps important et avoir un réel impact sur le planning du projet.
Conclusion
En conclusion, la conception et le lancement d’un projet industriel exigent une approche globale, intégrant les dimensions techniques, économiques et règlementaires. Alors que la définition minutieuse des composantes de l’usine établit les bases du projet, une vision holistique est primordiale pour optimiser les interfaces et favoriser la performance, l’efficacité et la rentabilité. Bien que le chemin vers la réalisation d’un tel projet puisse sembler semé d’embûches, une progression rigoureuse et méthodique permet de surmonter les obstacles progressivement.
Enfin, la conception d’une usine requiert non seulement une expertise pointue, mais également un certain recul. S’entourer des compétences externes nécessaires est ainsi essentiel pour assurer le succès du projet. Il est crucial de reconnaître que la construction et l’exploitation d’une usine exigent des compétences distinctes et une allocation de temps adéquate, ce qui peut être un défi pour les opérationnels déjà sollicités.
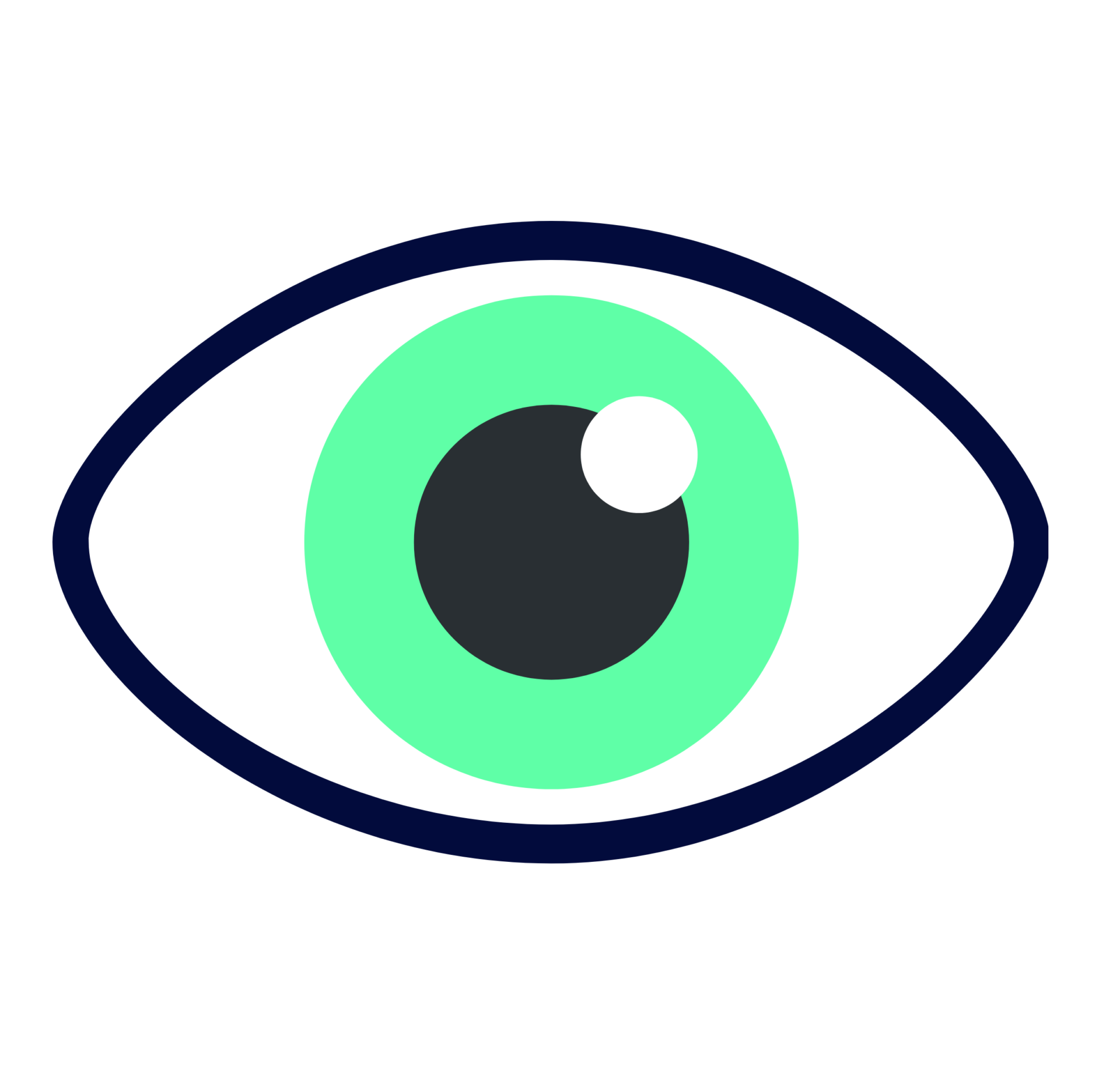
Que retenir ?
Choix du site
- Terrain à bâtir, bâtiments existants
- Dimensionnement, formes
- Environnement extérieur
Définition du process
- Stratégie de production (en ligne, par batch)
- Niveau d’automatisation
- Synoptique process (succession des opérations, dédoublement, environnement, goulets d’étranglement)
Définition de la logistique
- Mode de stockage
- Flux humains et marchandises
- Moyens de manutention
Organisation générale du site
- Capacitaire de l’outil
- Flexibilité de celui-ci vis-à-vis de la variation de la charge future
- Continuité de l’activité durant le projet industriel
- Imbrication des différentes zones pour optimiser les flux
- Flux intérieurs
Normes et réglementations
- Sécurité
- Environnement
- Règles d’urbanismes
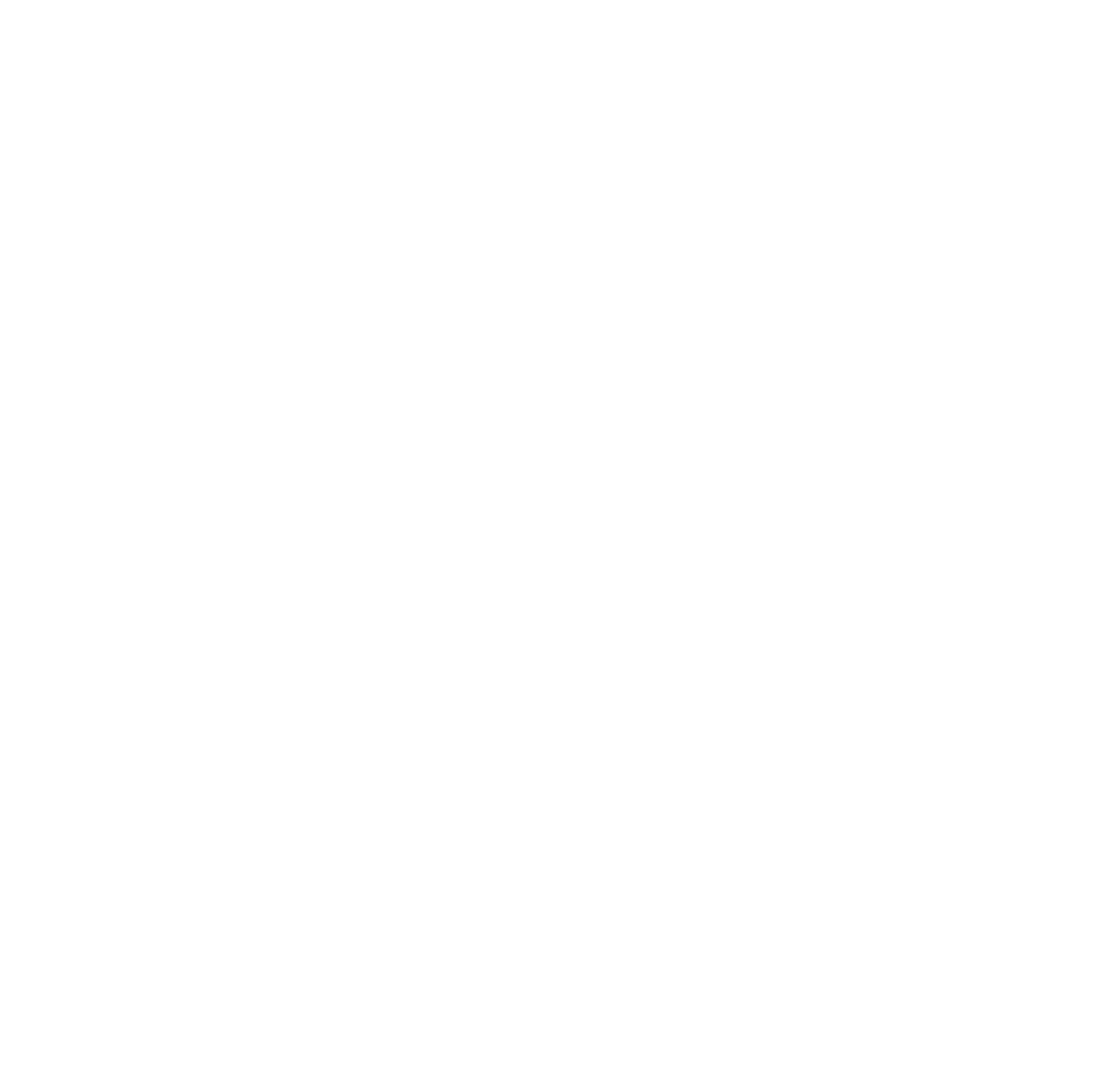
Etyo vous accompagne
La force d’Etyo pour vous accompagner dans votre projet industriel :
- Une vision stratégique couplée à des considérations opérationnelles : définir rigoureusement votre projet avec une vision globale, afin de garantir un système industriel performant.
- Un groupe aux multiples compétences dédiées à votre projet : savoir combiner les compétences en immobilier, supply chain et développement durable pour disposer d’une vision à 360°.
- Un conseil à valeur ajoutée : proposer des solutions innovantes, analyser vos modes de fonctionnement, amener de la hauteur de vue afin de vous aider à prendre les bonnes décisions.
- Un accompagnement sur le long terme : vous suivre tout au long de votre projet, jusqu’au démarrage de l’usine et à l’atteinte des performances définies.